China Gansu Network, March 14th (Northwest Corner · China Gansu Network
reporter Cheng Jian, correspondent Wang Yonghui) The reporter learned
from the No. 12 Oil Production Plant of Changqing Oilfield that as of
March 12th, the plant has carried out a comprehensive "spring
inspection" on personnel, stations, equipment and pipelines, and various
units have reported 236 self-inspection and self-examination problems.
This is one of the special actions of the plant to promote the
implementation of "There is no if in safety work, only results and
consequences" and safeguard the safety of spring production increase.
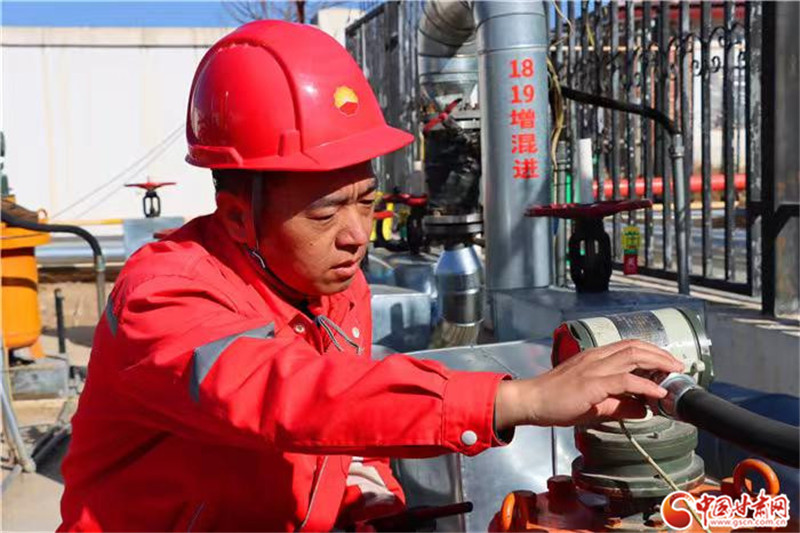
Since
entering March, with the rise in temperature, all work related to oil
and gas production has been fully initiated. The No. 12 Oil Production
Plant of Changqing Oilfield leads "stability throughout the year" with a
"stable start" in safe production, focusing on strengthening safety
management. It promotes on-site training of job operation cards, risk
identification cards, and emergency response cards with "technicians +
externally hired experts", and conducts regular random examinations
through the "1+2" supervision of the territorial units, business
departments, and site contractors. "Star-level employees" are evaluated
based on the assessment results, and rewards are implemented in
different steps, promoting the extension of safety training and safety
management to positions.
At
the same time, contractors are included in the training targets, and
the pre-entry training of contractors before entering the factory (site)
is strictly managed. A notification and exposure mechanism for typical
accidents is established, and combined with the problems investigated
and dealt with in the plant in recent years, safety training is carried
out targeted as a "living teaching material". Currently, a total of 124
various types of training sessions have been conducted throughout the
plant, involving 2,300 personnel.
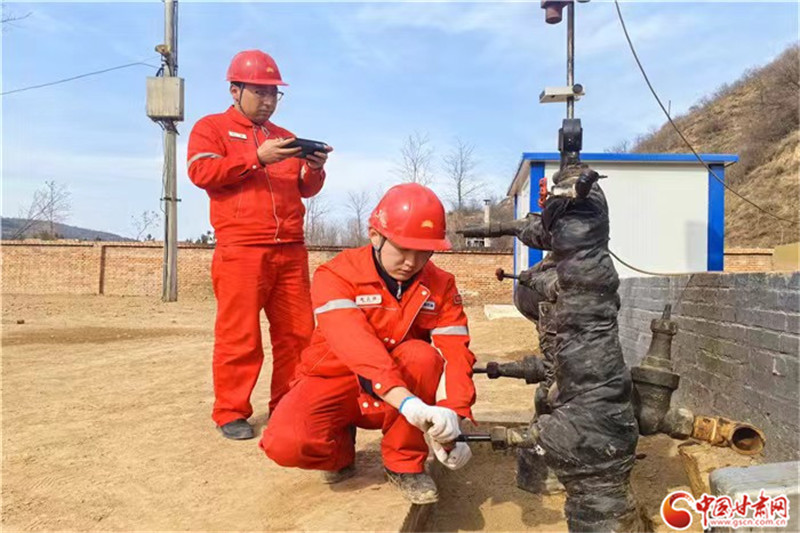
Centering on the annual production tasks, the entire plant has
established the principle that "not a single cubic meter of production
that is unsafe is wanted", and has taken on the sense of responsibility
of "curing the disease by scraping the bone" with the belief that "not
finding problems is the biggest problem". A four-level hidden danger
investigation grid system of "positions - teams - units - business
departments" has been established, the change management of third-party
employed personnel has been strengthened, and 3 - 5 "safety experts"
have been cultivated in each team. Through quarterly performance
evaluations, reaching standards for positions, and linking performance,
the goal of "professionals managing professional matters" has been
achieved.

Meanwhile,
in response to the warmer weather, personnel were organized to conduct
one-by-one inspections of site locations, oil and gas pipelines,
facilities and equipment, project starts, and low-lying and deeply
frozen areas. Daily risk warnings were issued, and weekly investigation
and rectification notifications were made, forming a closed-loop
management of hidden danger investigations.
"Through
various means such as on-site supervision, random phone checks, and
video reviews, it is ensured that on-duty personnel are aware of risks,
clear about their responsibilities, implement safety measures, and
operational risks are under control," said the person in charge of the
safety and environmental protection department of the plant. "Only
through strict management and strict investigation in safety work can
the inertial thinking of 'not being strict enough and not being
implemented' be changed."
At
the same time, through the "one theme per month" safety culture
activities, employees are guided to consciously practice safe production
behaviors. Since the beginning of this year, the entire plant has
carried out more than 80 safety and environmental protection experience
sharing sessions and 12 safety culture-themed lectures, with more than
2,000 participants.